|
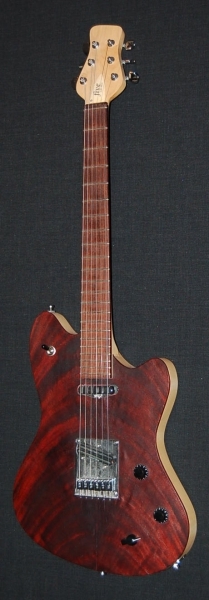 |
Technische Daten: |
Mensurlänge: |
628 mm |
Hals: |
Ahorn, geleimt Palisander Griffbret, mit 22 Bünden Nullbund |
Korpus: |
Ahorn mit Mahagonidecke, darauf ein gespiegeltes Pyramieden-Mahagoni Furnier |
Tonabnehmer: |
Bridge: SEYMOUR DUNCAN Hot Rails
Hals: ROCKINGER Telly Rhythm
|
Mechaniken: |
KLUSON Roundbacks |
Steg: |
Tele Bridge |
Bedienelemente: |
Ein Volumpoti fr jeden Tonabnehmer
und ein Ton-Poti für den Telly Rhythm
|
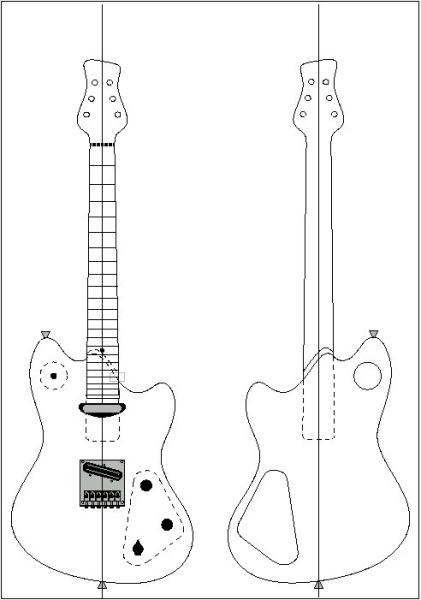 |
Die Verwendung einer aufgeleimten Decke
ermöglicht es mir, den Hals sehr weit in
den Korpus hineinreichen zu lassen, ohne
ein Schlagbrett benutzen zu müssen, welches
die Fräsarbeiten verdeckt.
Ich verspreche mir davon eine bessere
Leimverbindung, die ein längeres Ausschwingen
der Seiten unterstützt.
Vielleicht bringt es aber auch gar nichts.
|
Halsbau
Für die Halskonstruktion habe ich mich für eine angesetzte Kopfplatte entschieden. Dies soll Halsbrüchen
entgegenwirken, da der Faserverlauf des Holzes in Kopfplattenrichtung verläuft. Die folgende Skizze soll das
verdeutlichen:
|
Zu sehen ist der Halsrohling und meine Sägehilfe.
Die Sägehilfe besteht aus einer quadratischen Grundplatte
und ein im Winkel von ca. 15 Grad zur langen Seite der Grundplatte
aufgeschraubtes Brett.
|
|
Mit dieser Konstruktion ist es mir möglich, den Halsrohling
in dem von der Sägehilfe vorgegebenen Winkel durchzusägen,
indem ich die Sägehilfe parallel zum Sägeblatt
an einem Anschag entlang führe.
Na, wer findet den Fehler im Bild?
|
|
Die Schnittoberflächen sind nach diesem Vorgang leider noch nicht
so glatt, daß man sie verleimen könnte. Bei einem Früheren
Halsbau habe ich mal einen Halsrohling geschrottet, womit ich nun
für Schleifarbeiten eine geeignete Auf- und Unterlage habe, damit
die obere und untere Kante meines zukünftigen Halses nicht durch
abkippen meines Schleifblockes abgerundet werden..
|
|
Überprüfung des Ergebnises.
|
|
Zum Verleimen benutze ich meine Sägehilfe als Stütze.
Ich kann jedem nur empfehlen den Verspannvorgang einmal ohne
Leim zu proben, damit die Reihenfolge der Handgriffe klar ist,
wenn es ernst wird.
|
|
Über Nacht blieb das Ganze sich selbst überlassen und am
Morgen danach sieht der Hals nun so aus. Jetzt muß noch die Oberäche,
auf der das Griffbrett aufgeleimt wird, glatt geschliffen werden, da
ich es auch dieses mal nicht geschafft habe, die beiden Halsteile 100
prozentig anzupassen.
|
|
Nun ist der Hals grob zugeschnitten und die Griffbrettklebefläche sauber geschliffen.
|
|
Normalerweise würde ich die Nut für den Halsstab fräsen, bevor ich den
Hals grob zuschneide. Das erleichtert die Führung der Fräse. Aber da erst noch
die Oberfläche des Halses plan geschliffen werden mußte, habe ich den Hals schon
vorher zugeschnitten, um die Arbeitszeit zu verkürzen.
Somit mußte ich mir mit einem zweiten Stück Holz behelfen,
das als Anschlag diente.
|
|
Dieses Bild zeigt den Hals nach dem Ausfräsen der Halskontur
mit den dazu verwendeten Schablonen.
Dazu habe ich eine Fräse mit obenliegendem Anlauflager benutzt.
|
|
Fräse mit obenligendem Anlauflager zum kopieren der Form einer
Schablone auf das Werkstück.
|
|
Jetzt wird das Griffbrett aufgeleimt.
|
|
Das Griffbrett ist auf diesem Bild schon zurechtgeschnitten und auf Halsbreite geschliffen.
Mit einer in einen Bohrständer eingespannte Bohrmaschine, habe ich dann
die Löcher für die Dots am Griffbrettrand gebohrt.
|
|
Für die Dots habe ich einen Buchenstab mit einem Durchmesser von 3 mm benutzt.
|
|
Mit der Bandsäge sägte ich den Hals auf die richtige Dicke und
arbeitete dann die Rundung des Halses mit einer Holzfeile und 40er Schleifpapier heraus.
|
|
|
Nachdem der Hals seine endgültige Form hatte, schliff ich mit 80er Schleifpapier die Oberfläche
glatt. Der Feinschliff kommt erst, wenn alle anderen Arbeiten am Hals abgeschlossen sind.
Die Bohrungen für die Mechaniken sind auch schon gemacht.
Die Bundstäbe bekamen etwas Holzleim auf ihre "Nasen" und wurden mit einem Gummihammer eingeschlagen.
|
|
Vorher wurden die Griffbrettkanten mit auf einem abgerichteten Ahornvierkant (Halsreststück) aufgeklebtem Schleifpapier gleichmäßig
über die gesamte Griffbrettlänge abgerundet.
|
|
Mit einer bis zur Schnittkante abgeschliffenen Beißzange, hab ich die überstehenden Enden der Bundstäbe
abgekniffen. Dies erspart eine menge Schleifarbeit.
|
|
Die Kannten der Bundstäbe wurden auf die selbe Art und Weise wie die Griffbrettkannten behandelt.
|
Korpus
Die CA-Three war eigentlich nicht mit einem ausgehöhlten Body geplant, sondern sollte wie eine richtige
Semiakustik
werden. Hohl mit einer Decke und einem Boden. Somit waren noch zwei Mahagoniebrettchen übrig,
sowie genügend
Furnier. Dies ergab dann die unten abgebildete zukünftige Decke.
|
Die Ahornbohle lies ich vom Schreiner auf 40 mm abgerichten.
Nun konnte ich den Korpus mit der Bandsäge grob ausschneiden.
Dabei sollte man immer etwas Abstand zum aufgezeichneten Korpus halten, in diesem Fall
waren das im Durchschnitt ca. 3 mm.
|
|
Grob zugesägter Korpus.
|
|
Danach befestigte ich die Schablone mit zwei Schrauben auf dem Korpus.
Mit der Oberfräse kann nun der Korpus entsprechend der Vorgabe ausgefäst werden.
|
|
Hier kann man erkennen, wie das schaftseitige Anlauflager an der Schablone entlangeführt wird.
|
|
Für den nächsten Schritt entfernte ich die Schablone, damit auch der Rest weggefräst werden kann.
Jetzt dient der schon ausgefräste Teil als Schablone.
|
|
Wie man im obigen Bild sieht, bleibt noch ein Rest vom grob ausgesägten Korpus stehen. Da die Rückseite
eine verrundete Kante bekommen soll, drehte ich den Korpus einfach um und fräste mit einem Radienfräser
die Kante rund und im gleichen Zuge auch den überstehenden Rest weg.
|
|
Fertig ausgefräster Korpus.
|
|
Zur Herstellung der Schablone für die Halsauffräsung benutzte ich 2 Brettchen und
eine Leiste. Mit diesen wurde der Hals auf dem Schablonenholz eingefaßt. Somit erhalte ich
eine Führung für die Oberfräse.
|
|
Die Rundungen am Halsende bohrte ich mit einem Forstnerbohrer heraus.
|
|
Mit der Oberfräse kann nun die Schablone ausgeschnitten werden.
|
|
Das Fach für den Toggle Switch habe ich mit einem Forstnerbohrer ausgebohrt. Da ich mit der Fräße nicht
die koplette Dicke des Korpusses erfassen kann, steht ein kleiner Rand auf der Rückseite des E-Faches noch
über. Diesen werde ich wegfräsen, wenn die Vertiefung für den E-Fachdeckel gefräst wird..
|
Leimarbeiten
|
Hier wird der Hals mit dem Korpus verleimt.
|
|
Da der Hals dicker als die Halstasche tief ist, mußte das Überstehende mit der
Oberfräse abgefräst werden.
|
|
Korpus mit eingeleimten Hals und ausgefrästen Kabelschächten.
|
|
Beim Fräsen des Kabelschachtes war ich etwas übereifrig und mußte ein
Teil wieder ausfüllen, damit unter der Brücke kein Hohlraum ist. Ich wollte
vermeiden, das eine Schraube für die Brückenbefestigung auf diesen Hohlraum
trifft.
|
|
Grob ausgesägte Decke mit Aussparrung für das Griffbrett. Für die Aussparrung
habe ich die selbe Schablone wie für die Halstasche verwendet, in der ich einen
Anschlag für das Griffbrettende angebracht habe.
|
|
Aufleimen der Decke. Nach dem Aufleimen wurde der überstehende Rest der Decke mit der Oberfräse entfernt.
|
|
Vorne!
|
|
Hinten!
|
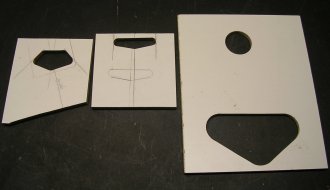 |
Hier habe ich mal die unterschiedlichen Schablonen für die finalen
Fräsarbeiten fotografiert. Zum ersten mal habe ich Abfallholz verwendet, welches
unser Baumarkt um die Ecke, umsonst zum Mitnehmen anbietet.
Es handelt sich hierbei um Pressspanbrettchen. Wie der Eine oder Andere vieleicht bemerkt
hat, habe ich für die
Halstaschenfräsung und den Hals selbst auch schon solche
Restbretter benutzt.
|
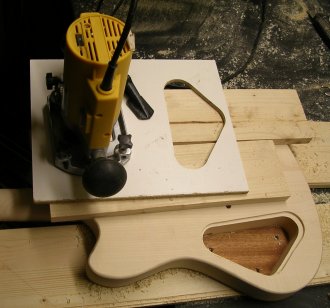 |
Was hier passiert kann man schlecht erkennen, aber es wird die Vertiefung für den Deckel
des Toggle-Switch-Faches gefräst.
|
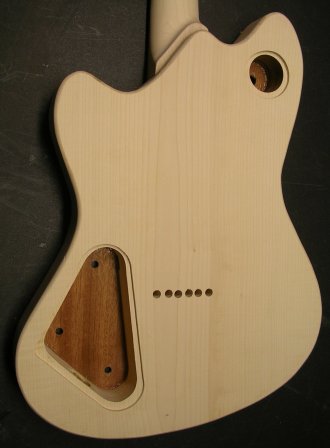 |
Fertig gefriäster Body von hinten.
Vielleicht kann man auch das Loch für die Klinkenbuchse erahnen?
Dieses wurde mit einem 25mm starken Forstnerbohrer gebohrt.
|
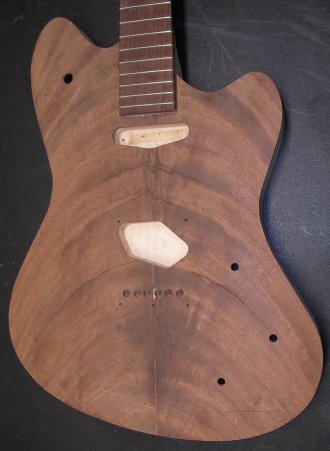 |
Fertig gefriäster Body von vorne.
|
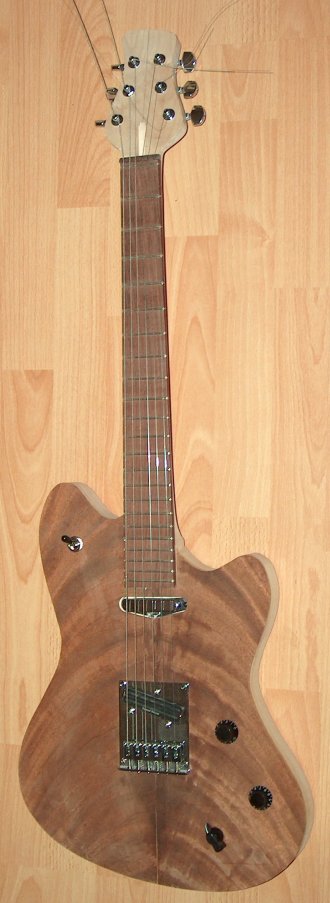 |
Die ersten Töne!!!!
Bin sehr zufrieden. Die Gitarre ist recht laut, die Seiten schwingen schiön lange
aus und es klingt irgendwie sehr ausgewogen. Mehr Soundbeschreibungen
möchte ich nicht von mir geben, da das doch jeder anders empfindet.
Nach reichlichem Testen beschloß ich, den Hals im Bereich des Überganges zur Kopfplatte
noch etwas zu optimieren. Ansonsten vermittelt mir die Gitarre
mit ihrem recht breiten und dicken Hals ein sehr gutes Spielgefühl.
|
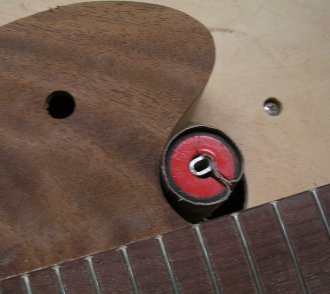 |
Nun folgt das endlose Schleifen! Für mich eine unangenehme Sache.
Zuerst schleife ich mit einem Schwingschleifer, mit unterschiedlichen Körnungen (max. 240er,
ist das feinste was ich momentan für den Schwingschleifer besitze).
Die Rundungen, die mit dem Schwingschleifer nicht erreicht werden können, Schleife ich
mit einer Schleifwalze. Danach mit der Hand mit 320er Papier.
|
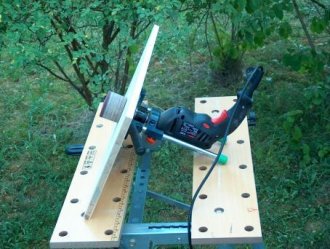 |
Mit dieser Konstruktion, wird die Schleifwalze betieben.
|
Die CA-FIVE bekommt eine rötlich Beize auf alle Mahagonieoberflächen. Die Schwierigkeit
dabei ist es, keine Beize auf das Ahorn zu bekommen. Da ich mit der CA-TWO schon solch
ein Vorhaben verfolgte, wußte ich um die Probleme. Hinzu kommt noch, daß wasserlösliche
Pigmentbeize nicht wischfest ist und beim Ölen wieder angelöst wird. Das bedeutet, die
Möglichkeit Pigmente ins Ahorn zu verwischen ist sehr groß. Da das damals eine Sauerei
und ein riesiger Aufwand war (mußte 2 mal wieder alles abschleifen), beschloß ich einen
Fachmann zu fragen. Ich ging zu Firma Rosner, welche alle möglichen Artikel zur Oberflächen-
behandlung für Hölzer herstellt und anbietet. Dort sprach ich dann mit einem Schreiner.
Er meinte, daß ich nie eine genaue Trennung von gebeizt und ungebeizt herstellen könnte.
Aber wenn ich es versuchen möchte sollte ich möglichst fein schleifen und die Fläche, welche
keine Farbe abbekommen soll mit Tesafilm abkleben. Auf die Frage, welche Beize ich nehmen
sollte, empfahl er mir eine pigmentfreie Mahagonibeize. Diese Beize ist nach dem Trocknen
wisch und kratzfest. Desweiteren empfahl er mir ein Wachs-Öl-Gemisch, welches oft für
Bodenversiegelungen benutzt wird und sehr hart aushärtet. Es kann im Abstand von 6 h der
zweite Auftrag (zwei genügen) erfolgen und nach dem Aushärten kann es auch noch Poliert werden.
Letztendlich zeigte er mir gebeitzte und gewachsölte (achtung Wortkreation!) Beispiele zum
Anfassen und an einem gebeizten Testholz auch noch, wie man das Wachs-Öl-Gemisch verarbeite.
Ich war völlig begeistert von der einfachen Verarbeitung und den Ergebnissen, so daß ich nur
einmal schluckte, als er mir den Preis für beides nannte, ca. 25,- Euro für Wach-Öl-Gemisch
(reicht bei zwei Aufträgen für 4,5 qm) und die Beize (1 Liter gebrauchsfertig).
So nun konnte ich, nach endlosem Schleifen, Wässern und wieder Schleifen, endlich mit dem Beizen
beginnen.
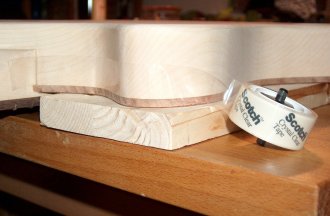 |
Also, empfohlen versucht!
Ahorn abkleben.
|
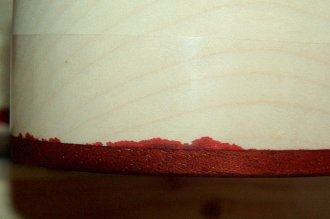 |
Und siehe da, Kollege Schreiner hatte recht.
|
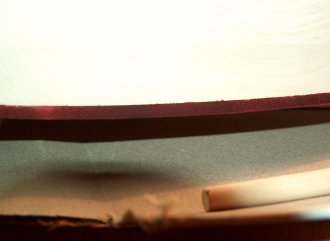 |
Aber mit ein bischchen Übung und weniger Beize am Pinsel sieht das doch schon recht gut aus.
|
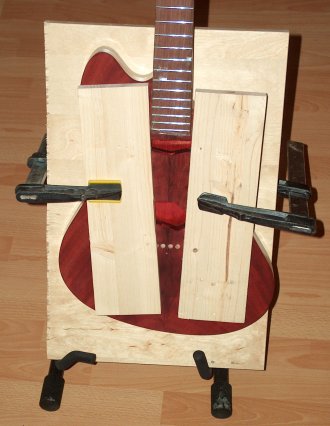 |
Nach dem Beizen kam der Schreck! Durch das Wässern der Oberfläche und durch die Beize,
hat sich das Furnier an manchen Stellen gelöst. Nach kurzer Überlegung (Leim feucht, löst
Furnier, Druck?, hm..., vielleicht klappts?) spannte ich den Korpus zwischen ein paar Bretter.
Nach einigen bangen Stunden, löste ich die Schraubzwingen und siehe da, der durch die Feuchtigkeit
angelöste Laim hat wieder geklebt. Mal sehen wie lange das hält!
|
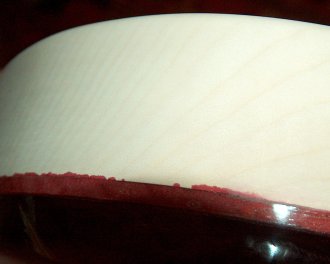 |
Nun versuchte ich die Beize vom Ahorn zu entfernen. Hierbei klebte ich den gebeizten
Teil ab.
|
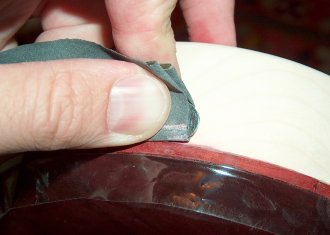 |
Mit um ein Besteckmesser gefaltetes 320er Schmirgelpapier schliff ich über die mit Beize
"befallenen" Stellen.
|
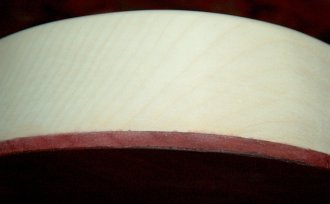 |
Das Ergebnis empfinde ich als zufriedenstellend.
|
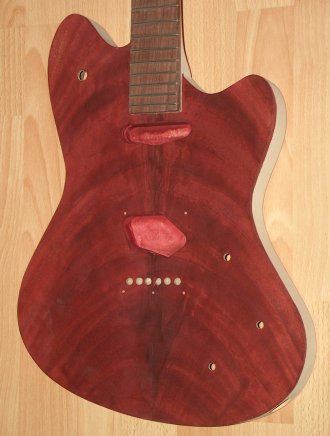 |
So sieht nun der gebeizte Korpus aus. Feucht sah das noch super aus, trocken eher
ernüchternd. Aber jetzt kommt das Öl ins spiel. Mal sehen wie es nach dem Ölen
aussehen wird.
|
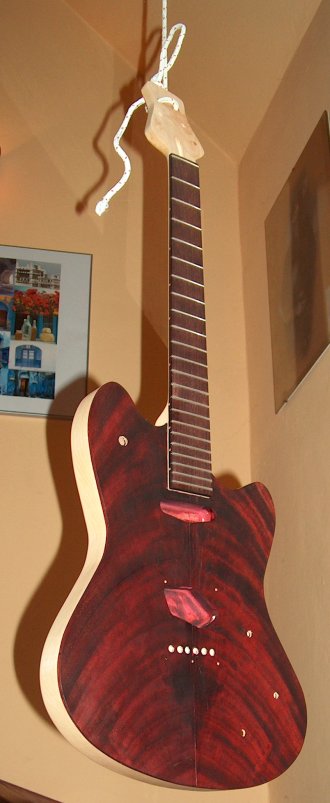 |
Nach langem hin und her Überlegen, befand ich die Beize für zu rot!
Daraufhin habe ich einen Rest Rockinger Öl, welches hauptsächlich nur
noch aus Wachs bestand, mit etwas schwarzer Beize gemischt. Das Wachs
war dabei etwas bröckelig, konnte aber mit einem Tuch sehr gut verrieben
werden. Die Ahornoberflächen bekamen eine Behandlung mit
Original Rockinger Öl. Dabei trug ich zwei mal im Abstand von 10 Min., das auf dem
Wachs schwimmende Öl mit einem Tuch auf und nach kräftigem Schütteln, 2 mal das Wachs-Öl Gemisch.
Danach kam das OSOMO Hartwachsöl. Dieses reibt man in zwei Arbeitsschritten im Abstand von
6 Stunden mit einem Tuch auf die Oberfläche. Nach dem Aushärten kann man die Oberfläche
mit Stahlwolle polieren. Ich habe 0000 Stahlwolle benutzt und bekam eine samtige, sehr
angenehm anzufassende Oberfläche. Super Produkt! Übrigens, die KKB Beize wurde während der
Behandlung mit den unterschiedlichen Ölen nicht angelöst und dadurch auch nicht verwischt!
Die KKB-Beize und das Hartwachsöl haben die Arbeit sehr vereinfacht und verkürtzt. Zusätzlich
habe ich damit, meiner Meinung nach, das bisher schönste Ergebnis erziehlt.
|
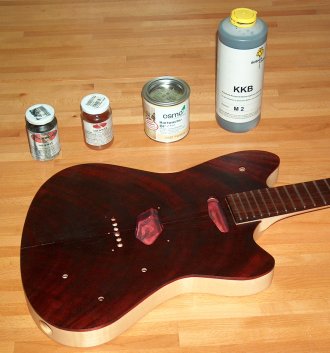 |
Die verwendeten Mittel zur Oberflächenbehandlung:
- Rockinger Öl gemischt mit schwartzer Beize
- Normales Rockinger Öl
- OSOMO Hartwachsöl
- KKB Beize
|
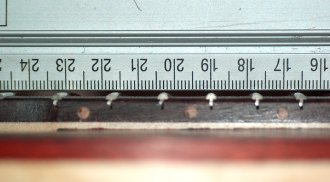 |
Wie man sehen kann, sind nicht alle Bünde gleich hoch.
|
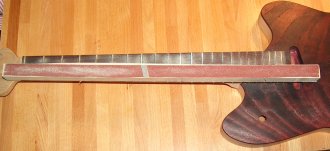 |
Mit einem auf einem abgerichteten Ahornvierkant geklebten Schmirgelpapier, werden
die Bundstäbe auf das gleiche Niveau gebracht.
|
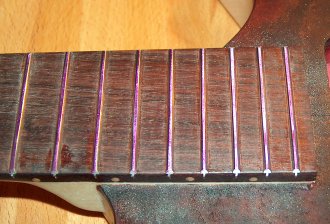 |
Die geraden Oberflächen makierte ich mit einem Textmarker.
|
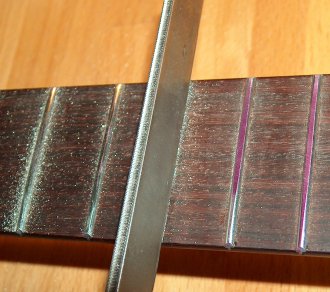 |
Mit einer Bundfeile, schliff ich die Bünde rund, so daß nur noch ein
schmaler Strich vom Textmarker übrig bleibt.
|
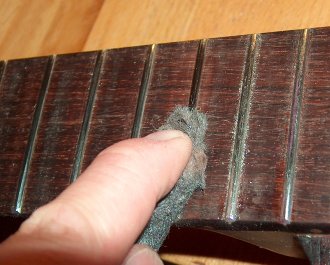 |
Zum schluß habe ich die Bünde mit Stahlwolle poliert.
|
Die Gitarre ist nun fertig. Fotografieren sollte ich aber noch ein wenig üben!
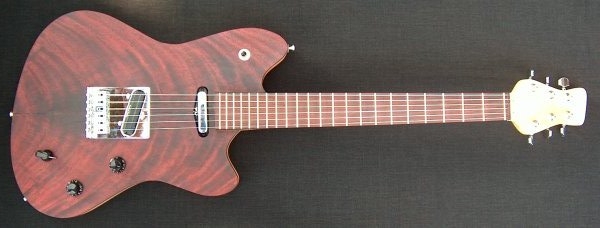
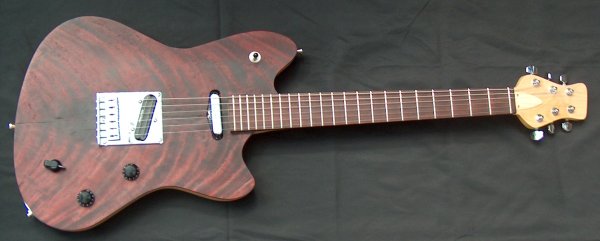
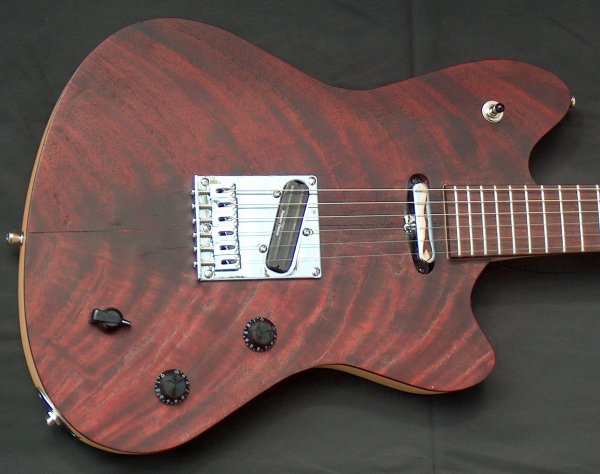
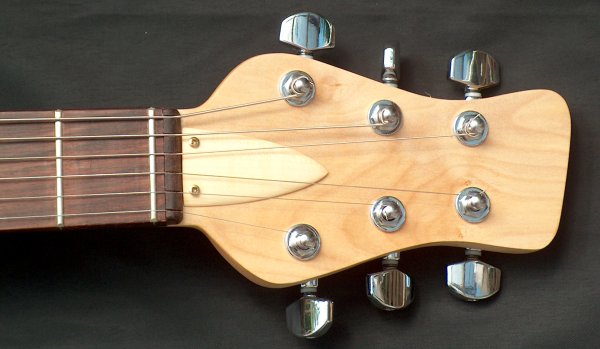
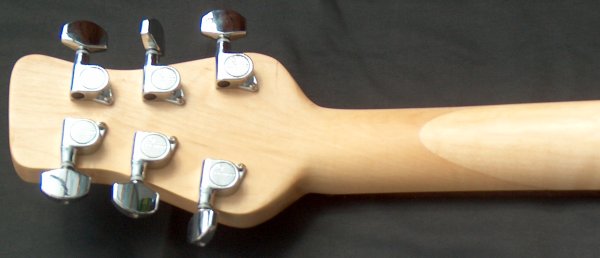
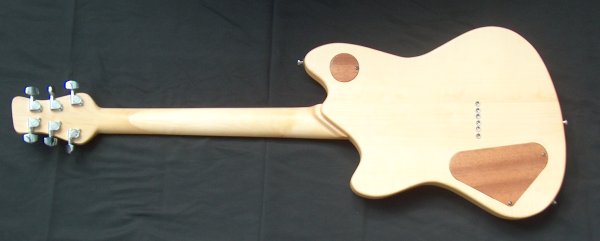
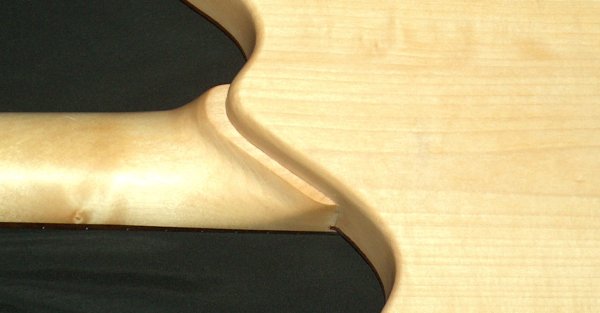
|